Engo GmbH
Fit for the future: Engo GmbH machines go digital with the help of a telematics solution.
Customer
Engo GmbH
Solution
Global Connectivity
Industry
Manufacturer of ice resurfacing machines
Initial Situation
Engo GmbH has been developing and producing ice resurfacing machines for rinks and arenas for 40 years. Since then, they have continuously expanded the performance and user-friendliness of their machines. Engo is a global company with headquarters in Italy. Before Engo installed Proemion's telematics solution, Engo faced repeated challenges with their existing remote solution because it could only send the collected data via Wi-Fi. They had technical problems with firewalls when connecting to stadium and ice rink networks. Also, their old solution’s availability was dependent on local Wi-Fi configuration settings that would change and require updates periodically, creating downtime. Aside from being inefficient and a source of frustration, Engo’s existing solution did not allow them to share data with their customers.
Features & Benefits
By implementing Proemion’s Global Connectivity solution, Engo makes itself independent of its client’s networks and WiFi and offers end-users access to all collected data. By equipping Engo's ice resurfacing machines with CANlink mobile 3000, data no longer needs to be sent over Wi-Fi networks. Instead, it’s sent to the DataPlatform via a cellular network. The cloud platform then forwards the processed data to the DataPortal, designed in Engo’s brand colors, via REST API. This solution enables Engo to offer an ideal fleet management system that displays data in real-time on an Engo-branded dashboard, shows security alerts directly on the web portal, and enables GPS positioning - when available. The bi-directional nature of the Global Connectivity solution enables remote diagnostics by allowing the Engo service team to connect directly to its machine.
Business Outcome
Before, only the technical department had access to the machine data. Now, Engo’s end-customers can also use it. In the digital age, when IoT is on everyone's lips, Engo can offer its customers a modern, digital telematics solution capable of displaying machine data on any device. The fleet management solution increases customer satisfaction and enables remote analysis and diagnosis of machine-status. Historical logged data is also used by engineers during the development of new projects, helping them optimize and expand Engo’s range of ice resurfacing machinery.
Questions?
Speak to an expert.
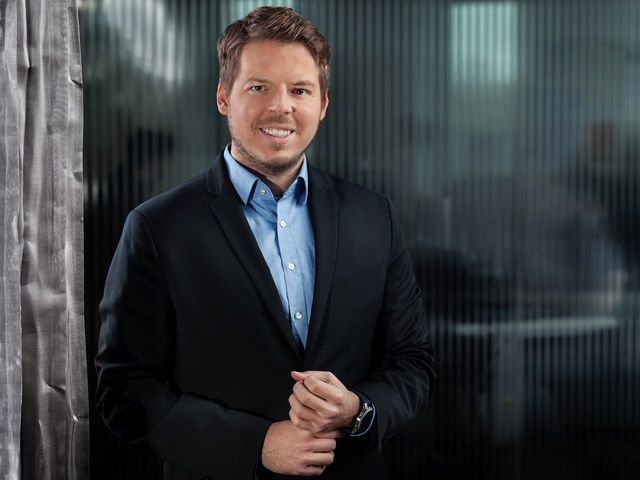