Cut costs and boost efficiency with Firmware-Over-The-Air (FOTA) updates
Are your customers waiting for technicians to travel onsite just to perform minor firmware updates? There is a better, faster, and more cost-effective way — Firmware-Over-The-Air (FOTA) updates. With FOTA, you can save money, improve service speed, and enhance customer satisfaction, all while staying ahead of the competition.
Onsite firmware updates drain time and money
Every time your technicians travel to update firmware onsite, you rack up unnecessary travel expenses and lose valuable time. Meanwhile, your customers are left waiting, sometimes with machines sitting idle, just to fix minor issues or receive the latest software improvements. The costs of travel, labor, and downtime add up quickly.
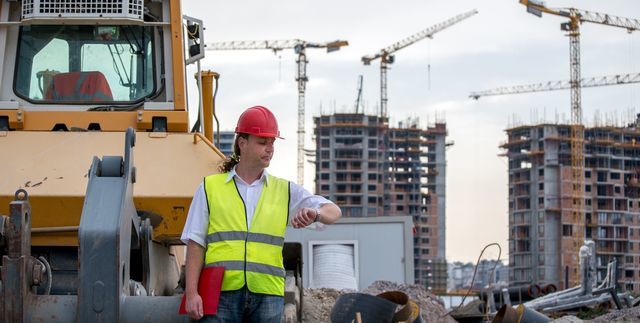
Update machines remotely, anytime, anywhere
With Firmware-Over-The-Air (FOTA), you can keep your customers' machines up to date without ever setting foot onsite. Using Proemion’s Global OEM Telematics solution, you can push firmware updates over the cellular network from anywhere in the world. This means faster updates, fewer travel expenses, and less downtime for your customers.
Not only do you save on travel and labor, but you can also offer customers ongoing improvements and even premium features with the click of a button. This flexibility allows you to provide a lifetime of value, helping to strengthen long-term relationships and keep your customers loyal.

Reduced costs and happier customers
- Cost savings:
Say goodbye to expensive service trips. On average, FOTA can save up to $1,200 per service case, slashing after-sales costs. - Increased efficiency:
Push updates instantly, reducing downtime and keeping machines running smoothly. - Stronger customer loyalty:
By offering ongoing firmware updates and premium features remotely, you can provide unmatched service that keeps your customers satisfied. - Competitive edge:
FOTA-enabled machines set you apart from competitors by offering faster, more convenient service, thus keeping your products at the cutting edge.
Savings per service case
This exemplary calculation includes typical service costs such as airfare, hotel, and service technician costs. It does not include the cost-specific impact of machine downtime on the machine owner's side
By embracing FOTA, you not only save money and time but also give your customers a seamless experience that builds trust and loyalty.