Dieci
Discover how Dieci secured its position as a leading manufacturer in the construction and agriculture sector with remote monitoring and excellent service.
Customer
Dieci s.r.l.
Solution
Global Connectivity
Industry
Telehandlers, Elevator, Truck mixer and Dumpers
Improve customer service and maintenance processes with a flexible telematics solution
Dieci, a leading construction and agricultural equipment manufacturer for more than 60 years, faced challenges in tracking and monitoring their machines worldwide. They needed a telematics solution to enable remote access for after-sales and technical purposes. With a diverse range of machines and custom solutions, monitoring and maintaining their fleet was complex. Dieci aimed to improve customer service, reduce machine downtime, and optimize maintenance processes. Therefore, they sought a solution that could provide real-time monitoring, diagnostics, and remote servicing capabilities.
On the quest to find a global machine monitoring solution for their worldwide customers
Dieci encountered several operational challenges that posed significant hurdles. One of the primary difficulties arose from the fact that most of their machines were sold and utilized in foreign markets. This widespread distribution made tracking and monitoring the machines a complex task, requiring close collaboration with dealers to overcome logistical obstacles. Additionally, Dieci faced issues stemming from the absence of an advanced diagnostic system. Without such a system in place, providing efficient customer service became a challenge, resulting in increased machine downtime. The existing process relied heavily on on-site service, which proved costly and time-consuming, leading to longer service times and delayed customer response times.
Furthermore, Dieci's commitment to delivering customized solutions based on customers' specific technical requirements further complicated the monitoring process, necessitating a more comprehensive and flexible fleet management system. The absence of advanced diagnostics impacted customer service and hindered Dieci's ability to guarantee maximum productivity of their vehicles and minimize machine downtime. Customer service was primarily conducted on-site, where customers would send photos or videos to the dealers to request intervention. This approach gave rise to several critical issues, including high service costs, multiple technician visits to address problems, extended service and response times, and the need for a vast network of technicians to ensure swift and efficient on-site service. Moreover, the complex and evolving nature of Dieci's product range often rendered formal training and manuals insufficient in assisting customers, necessitating a more advanced solution.
A comprehensive and flexible solution that complies with Danfoss and the Italian Industry 4.0 initiative
Faced with these operational challenges Dieci decided to implement Proemion's Global Telematics solution for OEMs. This decision was driven by Proemion's industry leadership, strong commitment to service quality, and partnership with Danfoss, a major component provider for Dieci's machines. The comprehensive solution consisted of CANlink® mobile Var. PLUS+1, Dataplatform, and DataPortal, offering robust monitoring and data management capabilities. In addition, Dieci closely collaborated with Proemion to tailor the software to their specific needs, utilizing REST API for seamless data transmission.
Dieci's decision to adopt Proemion's telematics solution was also motivated by the fiscal benefits offered by Industry 4.0 initiatives in Italy. Recognizing the long-term value and future growth potential, Dieci strategically invested in an advanced telematics solution. This positioned them at the forefront of the telehandler market, ready to meet customer demands and embrace the opportunities presented by Industry 4.0. Through their collaboration with Proemion, Dieci gained a comprehensive and tailored monitoring system, enabling efficient fleet management, proactive maintenance, and effective utilization of their machines.
20% travel costs saved, machine downtime reduced by 30%
Dieci's implementation of Proemion's Global Telematics solution for OEMs resulted in significant benefits for the company. With real-time monitoring, remote servicing capabilities, and advanced diagnostics, their customer service improved significantly, reducing machine downtime by 30%, and increasing the number of cases solved remotely by 25%, which also led to saving 20% on travel costs. Moreover, Dieci leveraged Proemion's partnership with Danfoss, gaining access to crucial intellectual property that set them apart from competitors. This integration allowed Dieci to fully leverage the capabilities and functionalities of Danfoss components within the telematics solution, further enhancing performance and functionality.
The integration of Proemion's telematics system with SAP has significantly improved Dieci's internal processes, aligning seamlessly with the requirements of Industria 4.0. This integration places Dieci at the forefront of technological innovation and brings operational efficiency. Compliance with Industria 4.0 standards has not only accelerated Dieci's operations but has also positioned them for fiscal benefits outlined by the Italian government. This financial advantage serves as a significant boost for Dieci and its customers, highlighting the diverse benefits of Proemion's telematics solution in fostering a forward-looking and financially prudent operational environment.
The telematics solution not only enabled Dieci to monitor and diagnose machines worldwide, optimize maintenance operations, and improve efficiency but also played a crucial role in their vehicle development. By utilizing monitoring systems, they can assess vehicle usage and identify recurring failures, leading to product enhancements and reduced issues. Additionally, Dieci's engineers leverage remote monitoring to analyze new product development during testing, resulting in improved development efficiency and a shorter time to market. Telematics, therefore, plays a crucial role in providing clear information and insights for Dieci's future advancements. Moreover, by integrating telematics into their vehicle development process, they ensure that future machines will be equipped with advanced telematics capabilities.
The positive results and sector development are expected to increase the number of machines sold with telematics services internationally, cementing Dieci's position as a leader in the construction and agricultural equipment market.
We produce increasingly sophisticated and safe machines. Identifying problems and providing assistance becomes increasingly complex. Introducing a system that would help service, dealer, and engineering was essential. Thanks to telematics integration, we are connected to our machines and our dealer networks. This allows us to respond efficiently and quickly to requests by providing professional service.
You want to learn how our solution can add value to your business?
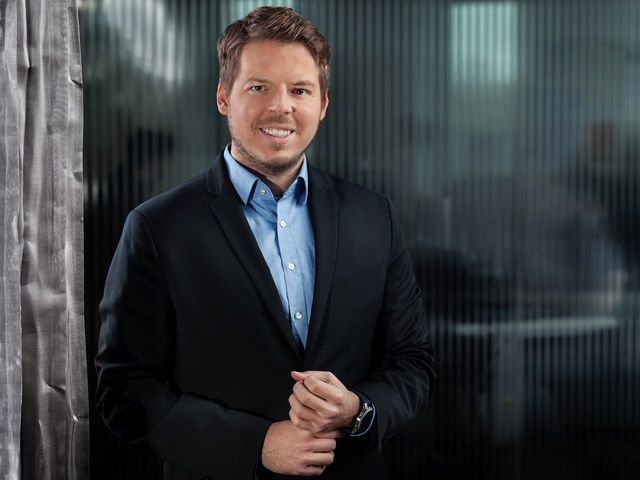