A step-by-step guide to implementing a unified mixed fleet solution
Executive Summary
The construction industry is slow to adopt the telematics solutions offered by heavy equipment OEMs, even though their data promises a significant advantage over paper-based systems.
This white paper explored the ISO 15143-3/AEMP 2.0 communication standard developed by the Association of Equipment Management Professionals (AEMP). This standard allows construction companies to “connect” their telematics systems without investing in additional hardware.
We discussed data quality issues across different OEMs, across different machine models from the same OEM, and the effects of data frequency availability.
The whitepaper laid out a 3-phase implementation roadmap consisting of Gather & Sanitize, Integrate & Synchronize, and Operate.
Finally, we considered data protection and ensuring compliance with current data protection legislation (GDPR), including some challenges and recommendations to help keep you compliant.
We concluded that implementing a digital mixed fleet telematics solution was not time-consuming nor difficult. Using the Association of Equipment Management Professionals (AEMP) communication standard as your foundation, it was a straightforward 3-phase process outlined in our roadmap.
Introduction
The construction industry operates with razor-thin margins, and miscalculations of operating costs and unexpected downtime can significantly affect profits and customer satisfaction. Typically, construction fleet owners work on multiple projects at once. Therefore, if a piece of equipment breaks down, it can lead to missed deadlines on the initial project with rippling effects that impact other projects that might need that equipment or the operator’s time. Breakdowns also include the costs associated with equipment rentals or urgent repairs.
The effective use of construction equipment significantly impacts the cost and schedule of building projects and the opportunity to increase productivity. Machine IoT (telematics) enables higher operational efficiencies that are difficult to achieve with traditional manual systems.
Telematics systems work by connecting a device, such as a GPS tracker or other data logging tool, to an asset. The tool collects key performance data about the asset, and the device then sends the information to a data center where it’s collated, interpreted, and analyzed.
Today, most heavy equipment manufacturers (OEMs) provide a telematics system with their equipment. However, OEMs have different approaches to the type of data they collect and make available, and often OEM telematics systems don’t interact with one another.
As a result, construction companies operating a mixed fleet of machines struggle with different OEM solutions and getting a complete view of their fleet, leading to duplicated effort when integrating machine data into their systems.
Alternatively, construction companies decide not to use available technology as the many alternatives preclude meaningful use. While acknowledging the cost of managing the workforce with paper, the cost and risk of implementing a new system with unclear use cases are deemed higher.
This whitepaper explains how companies can overcome the lack of interoperability of OEM telematics systems and implement a mixed fleet telematics solution.
The Problem
Nowadays, construction companies face difficult decisions when it comes to available telematics solutions.
Either accept their organization must use and integrate multiple OEM telematics systems to get the job done or decide against using the technology available to them - both options have their drawbacks.
Countless studies and surveys have shown that business owners continue to underinvest in technology, despite acknowledging the many benefits it can provide in running their business and managing construction projects. For example, this McKinsey insight describes the construction industry as “among the least digitized sectors in the world,” citing MGI’s digitization index as proof of this.
Even when technology is employed, it’s often fragmented, which results in equipment owners having to check a variety of portals to collate the information necessary for informed decision-making.
What’s causing this behavior?
In an industry so focused on “time and materials,” changes that require investment outside the scope of a project, or fail to deliver to project timelines, may get dropped quickly or fail to be adopted at all.
Additionally, we often hear that decision-makers are unclear about what a transformation should accomplish, and it is clear there is poor integration of digital tools with business processes.
A High-Level Solution
Telematics solves most issues construction companies maintaining paper-based processes face. However, it creates new challenges for organizations that operate a mixed branded fleet of machines as OEM telematics don’t integrate with each other.
The lack of interoperability between OEM telematics systems was recognized by the Association of Equipment Management Professionals (AEMP) - an organization serving those who manage and maintain heavy off-road fleets as well as equipment in general.
They developed a standard that specifies “the communication schema to provide mobile machinery status data from a telematics provider’s server to third-party client applications via the Internet.” This standard, originally known as ISO 15143-3, is also described as AEMP 2.0.
One of the main benefits of this approach is that construction companies can reuse their existing telematics and IoT inventory without investing in additional hardware.
Additionally, one integration can fit all OEMs, unlike the previous situation where it was necessary to build an integration for each OEM.
Because the communication schema needs to support machine data for various machines, and telematics systems are of different maturity levels, the amount of data made available via ISO 15143-3/AEMP 2.0 is limited.
The situation is further complicated by OEMs implementing the standard slightly differently from one another and the schema providing a limited number of signals to work with.
Despite these limitations, new values can be calculated based on existing signals. The ISO 15143-3/AEMP 2.0 standard defines all the data presented in this table.
Meta Data | Data | Errors & Warnings |
---|---|---|
Machine IDs (VIN/PIN) | Location | Fault Codes |
Machine Manufacture | Fuel used | Error Codes |
Machine Model | Fuel remaining | |
Equipment ID | Operation Hours | |
Idel Hours | ||
DEF remaining | ||
Average Engine Load Factor |
Data quality of signals shared by OEMs
While ISO 15143-3/AEMP 2.0 is a standard, our analysis shows there’s still a lot of inconsistency across OEMs in the provisioning of information for their various machine models (see image 1.0).
There are also data quality issues across OEMs due to each implementing the standard differently - even across the various machine models from the same OEM. An OEM may provide specific signals for some models but different signals for others.
Beyond the inconsistency of data, the frequency of data being made available also influences the quality of machine data. For example, as shown in image 1.1, OEMs have very different intervals for specific signals.
Imagine if fuel level signals are only sent every 24 hours; how would a company design a reliable process around the refueling of machines? Similarly, in the case of machine location, it’s crucial to have frequent updates to keep track of where machines are for refueling, maintenance, and machine re-location purposes.
Fuel Management and invoice reconciliation
- Signals used: Fuel level, fuel used
- Signal Frequency recommended: max every 15 minutes.
- Frequent updates of fuel levels for each machine on a job site can help you monitor which machines have upcoming refueling needs.
- You can automate these fuel orders with your supplier, including the delivery schedule.
- Invoice reconciliation through fuel order, supplier bill, and actual fuel level of the machine is possible.
Next, we’ll explore a 3-phase implementation roadmap for a unified telematics solution.
Getting Started
An implementation roadmap is one of the most critical aspects of putting a unified telematics solution in place. A unified solution helps you start optimizing your business and working more effectively.
In the detailed roadmap that follows, you’ll see it consists of three phases – Gather & Sanitize, Integrate & Synchronize, and Operate. These phases are implemented in order and incrementally.
Meanwhile, there’s an ongoing legal requirement to ensure your solution complies with the General Data Protection Regulation (GDPR) applicable in Europe, which runs parallel with the iteration of these three phases.
Phase I – Gather & Sanitize
In the Gather phase (also known as the discovery phase), you start to identify the machines you’re going to select to work. You initially approach this integration with several OEM machines chosen instead of the whole fleet at once.
Before considering any signals received, you need to assign global IDs to your machines to enable you to check your inventory against what has been supplied by OEMs.
However, you will be able to structure the machines in your system to map your organization only when your inventory is validated and you’ve carried out the following checks:
- Do the machines my OEM says are delivered exist in my inventory?
- Have I received machines that are not in my inventory?
- Are machines received but not in my inventory, mine, or an error?
- Is my inventory wrong?
- Can I access all the machines I want to target in this phase?
You need to ensure you can access and retain control over all your fleet’s data.
For each OEM’s telematics solution:
- Connect your OEM’s AEMP interface to your Mixed Fleet Data Hub.
- You’ll need to provide the URL of the service and the access credentials.
- Sanitize your machine inventory.
- Once your inventory is sanitized, remove equipment that no longer exists in your fleet to avoid friction downstream in your business processes.
- Delete information from machines you don’t own to be compliant with GDPR.
Gathering your machine inventory and sanitizing it thoroughly in this way provides the basis for maximizing the benefits you’ll receive from your unified solution for mixed fleet telematics.
Questions to ask yourself:
- How does an inaccurate inventory impact my business?
- What are the key business improvements that good inventory management drives?
Understanding your fleet's reality
It’s crucial to establish an accurate fleet inventory and keep it up to date; here are some steps you can take:
- Set up unique global IDs for your machines across systems.
- Use your internal ID regardless of OEM IDs.
- Automate the maintenance of these IDs in just one system (it’s hard to keep track of global IDs manually across systems from different OEMs).
- Integrate your Mixed Fleet Data Hub with your inventory system.
- Identify missing machines and update your inventory.
Then…
Establish policies and automated procedures to keep your machine inventory up to date based on facts retrieved from the Mixed Fleet Data Hub.
- Structure your fleet to map your business (optional).
- Identify business unit ownership of machines and worksites where machines are assigned.
- Keep your inventory healthy.
Phase II - Integrate & Synchronize
In phase I, most of the focus is on metadata:
- Whether you have a machine or not.
- Can you identify the types of equipment you have?
- Can you reconcile machines in your inventory with machine IDs coming in from your integration?
When Phase I is complete, your machine inventory has been sanitized, and machines that no longer exist have been removed. It’s now time to connect all OEM’s AEMP interfaces to your Mixed Fleet Data Hub and move to Phase II.
In phase II, we focus on gathering signal data - what signals we get for each OEM machine and model and how frequently we receive updates. Again, we need to understand the quality to understand what use cases we can unlock.
In this phase, we can provide evidence of data quality issues so the customer can talk to OEMs and request improvements.
Phase II is considered complete when your unified mixed fleet telematics solution is in place, and all integrations are working correctly. You’ll also be able to integrate with your ERP system. This is the last step before starting to operate your solution.
Phase III - Operate
With Phases I and II in place, your inventory data is sanitized, integrated, and synced. It’s now time to move to phase III and ensure a unified view of all machines through good inventory management.
You’ll now be able to see all the information defined in phases I and II in a single place. Below you can see some of the benefits of having your mixed fleet telematics solution in place.
Machine location:
- Protect machines from theft.
- Ensure proper job documentation is in place.
- Record machines’ locations at worksites.
- Document all machine movements between worksites.
Efficiency:
- Ensure optimal fuel efficiency.
- Ensure efficiency of hours worked.
- Plan for required capacity.
Data:
- Back up regularly and test backups.
- Protect your data.
Activity:
- Record machine utilization.
- Detect misuse of machines, including excessive idling.
- Document fuel usage at each location.
- Manage operating expenses.
- Monitor C02 footprint.
Maintenance:
- Maintain good fleet health.
- Extend the life of machines.
- Reduce maintenance costs.
- Ensure higher residual value of machines for increased ROI.
Meeting the data protection challenge
Ensuring compliance with current data protection legislation (GDPR) is critical during the whole operational phase. Here are some challenges and recommendations to help keep you compliant.
Machine data can be personalized (de-anonymized)
Challenge:
Using a machine operator’s name or personnel number in digital workflows, combined with data such as machine ID, its condition, or performance, can quickly personalize seemingly anonymous data. In addition, linking machine movements and personal data can create tracking profiles for individuals.
Mitigated by:
Check which business processes have an absolute operational interest and which do not – employ principles of data economy.
Challenge:
Regulate data processing, not only in-house but with service providers and manufacturers.
Mitigated by:
Investigate who’s involved in data processing in-house and elsewhere - how are they affected and why? How can you ensure data processing complies with the required standards and legal requirements?
General recommendations
- Involve your Data Protection Officer from day one.
- Get consent from employee representatives.
- Put contractual agreements for data processing in place.
- Comply with General Data Protection Regulation art.13 (DSGVO).
- Be transparent from the start and at all times.
Conclusion – implementing a digital mixed fleet telematics solution is straightforward
This white paper has outlined how you can exploit available technology and implement a unified machine telematics solution in your organization while remaining compliant with GDPR.
Indeed, introducing such a solution to your company can take your daily work tasks to a whole new level of efficiency and accuracy, thereby delivering tangible value back to the business.
As a bonus, you’ll no longer have to check a variety of portals to collate the information necessary for informed decision-making.
Using the Association of Equipment Management Professionals (AEMP) communication standard as your foundation, it’s possible to connect diverse telematics systems without the need to invest in additional hardware.
Implementing a solution is not time-consuming nor difficult - it’s a three-step process as outlined in this white paper.
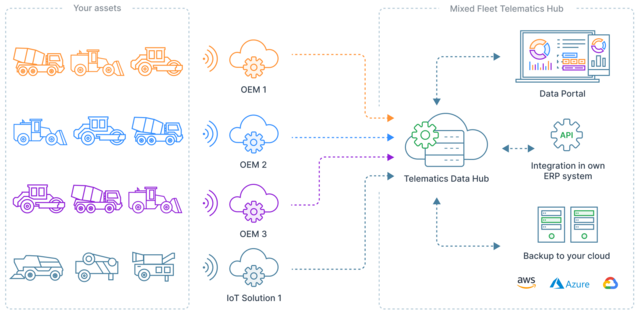
The benefits of not having to check different telematics portals to get information about your equipment and replacing outdated paper-based systems with a digital solution far outweigh the effort involved.
So, now that you know more about implementing a unified view of your mixed fleet, contact us and stop checking multiple telematics portals to collect the simplest information from your equipment.
Tired of checking different telematics portals?
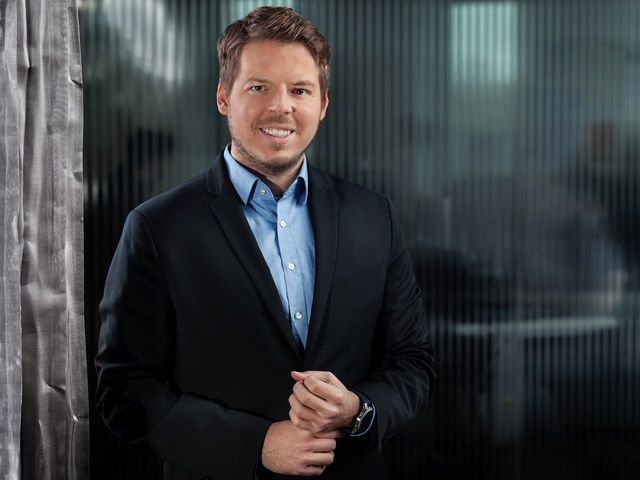