Cut service travel costs by 20-30% with remote diagnostics
Traditional service diagnostics require technicians to be physically present at the machine's location, using a direct cable connection to analyze issues. This approach not only drives up travel and labor costs but also keeps customers waiting, sometimes longer than necessary. The solution? Remote service, which slashes costs and boosts customer satisfaction.
Onsite service leads to high, unnecessary costs
Without remote diagnostics, many OEMs face inefficient service processes. Technicians often arrive at a job site without knowing the full scope of the problem, leading to delays when additional parts or tools are needed. Worse, unforeseen complications can prolong visits, throwing off schedules and frustrating both customers and service teams.

For OEMs, these delays and inefficiencies lead to high after-sales costs and a dip in customer satisfaction. For machine owners, the cost is even greater—extended downtime means lost productivity and revenue.
Remote diagnostics that keep machines running and customers happy
By integrating remote service into your workflow, you give your technicians the power to connect with machines from anywhere. Proemion’s telematics solution, powered by a complete platform from the CANlink® mobile TCU to the DataPlatform, allows service technicians to remotely access the machine’s ECU and perform diagnostics without leaving the office.
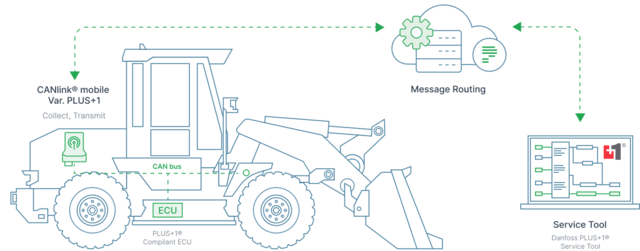
This remote access means technicians can instantly assess issues, identify problems while the machine is still running, and respond to service requests faster than ever before. Your customers benefit from reduced downtime, quicker resolutions, and improved overall service. For your business, it means fewer trips and lower costs.
Seamless service, lower costs, and happier customers
Using Proemion’s Global OEM Telematics or integrating it with your existing diagnostic tools (like Danfoss PLUS+1® Service Tool), you can remotely monitor and manage machine data, allowing your technicians to:
- Diagnose issues faster, often without needing to be on-site.
- Better plan staffing and spare part inventories.
- Minimize costly technician training by focusing on a specialized remote service team.
By adopting remote diagnostics, OEMs can reduce services travel costs by 20-30% and elevate their customer service experience, helping you stay ahead in a competitive market. Save time, reduce costs, and keep machines running smoothly—all while strengthening customer relationships.