Maintenance Tasks
Benefit from consistent documentation and increased after-sales revenue opportunities
Paper-based maintenance plans and records are more guess-work than facts
Machine owners have a huge interest in extending the lifetime of each machine and avoiding unnecessary, costly repairs and business-interrupting machine downtime. For OEMs, it's also essential to have a transparent overview of maintenance work to know which maintenance tasks are planned or performed for machines.
Paper-based or semi-digital maintenance planning processes bring many disadvantages: sometimes, upcoming maintenance tasks are missed because of unreliable communication channels to relay the maintenance information. The results are often unnecessary machine downtime, high repair costs, and unsatisfied customers.
Replace unreliable paper-based maintenance processes with a digitized workflow
The DataPortal and DataPlatform allow you to implement machine data-based maintenance tasks based on your regular maintenance schedules. This allows OEMs to transform their paper-based documentation processes into seamless, digital documentation.
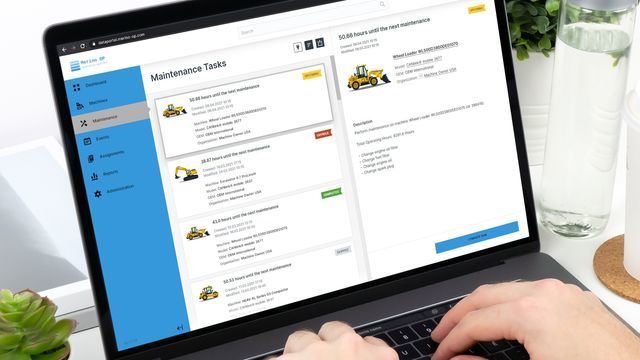
What information is needed?
The parameters can be aligned to your requirements: Define service cycles based on your maintenance booklet or service manual with fixed or floating parameters, such as machine operating hours or distance traveled (km or mi).
In a small workshop, we discuss all the essential parameters with you and how we can integrate the feature into your processes.
Two options to start with Maintenance Tasks Feature
Option 1: Use Proemion's DataPortal
You can use our DataPortal to get an overview and total transparency about all maintenance tasks. An OEM-tailored logic is continuously checking your machine data and creating the tasks.
The maintenance tasks can have different states, such as Upcoming, Skipped, Overdue, and Completed:
- Upcoming: A new maintenance task is coming up (i.e. a defined number of operating hours before).
- Overdue: The task was not handled during the expected time range.
- Skipped: The overdue task was not handled before a new upcoming task. Therefore, the overdue task is skipped.
- Completed: The maintenance was performed.
The interface gives you the option to filter and sort the tasks according to the state, organization, machine, or model. You can even print or export (CSV file) the list of tasks.
Subscribe to Maintenance Tasks and receive a weekly summary about the current maintenance schedule for your machine fleet.
You want your dealers to enhance communication with machine owners? Then give your dealers access to the maintenance feature so they can enforce their interactions with customers.
Option 2: Use the tool you already have
Use the DataPlatform's API to generate automated maintenance tasks in your existing maintenance ticket system or another system.
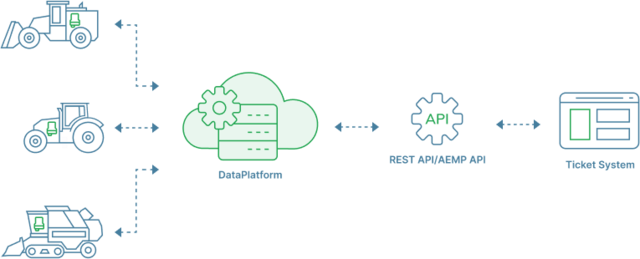
If you want to use your existing ticket system for maintenance management, it can automatically request information from Proemion's DataPlatform to create new maintenance tasks or tickets based on processed machine data.
Start to digitize your maintenance process
Implementing the Maintenance Tasks Feature can bring OEMs many advantages and opportunities, such as:
- Increase the communication with your customers and contact them proactively to schedule maintenance tasks
- Improve your documentation process with a digitized workflow
- Support your customers with keeping their machines operational and avoiding costly repairs
- Increase sales of spare parts and consumables
- Create higher workshop turnover for your dealers
- Strengthen your customers' satisfaction with your after-sales services
Still have questions?
Do not hesitate to contact us!
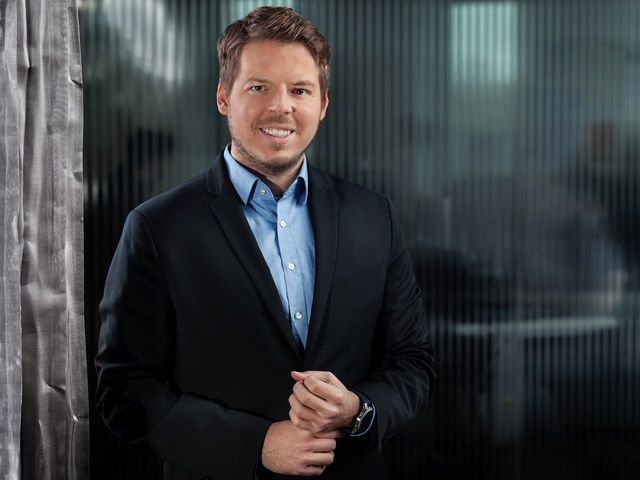
Discover how these OEMs benefit from a digitized maintenance process
Read more about how to support customers with fighting machine downtime
Online maintenance planning reduces machine downtime up to 50%
Help your customers get rid of paper-based maintenance plans and documentation by offering them a digitized maintenance process to keep their machines operational.